Become a Lean Machine With These Top 8 Lean Tools (Free Templates)
Blog: The Process Street Blog
Studies show that moving towards a leaner business model can improve productivity by up to 25%, increase stock turnover by 33%, and increase on-time delivery by 26%.
The recognized benefits of being lean are only accumulating, with more and more studies advocating lean approaches in business for both economical and sustainable success.
However, some companies choose not to embrace lean philosophy through fear that the costs related outweigh the benefits gained. With this, we at Process Street have come to help.
You see, this fear has oozed from imperfect implementation and a misunderstanding. With the right lean tools and techniques, lean thinking can easily and successfully be applied.
In this article, we present you with our top 8 lean tools to assist you in implementing lean philosophy for your business or line of work. By using these tools, you will see a transformation, with maximal value and minimal waste.
Along with these tools, we grant you access to our template resources, which you can hop in and use right away for free. For a quick taster, check out our ISO 9000 Structure Template embedded below.
Click here to access our ISO 9000 Structure Template!
Click on the relevant subheaders below to read the section of choice, alternatively scroll down for all I have to say.
- What is lean?
- The 5 lean principles
- Lean tools: Our top 8 lean tools to assist lean principle application
- Lean tools and the benefits they give
- Process Street and Zapier: Lean software tools you should use today
Keen to become lean? Let’s jump in!
What is lean?
To be lean in business means to maximize stakeholder value and minimize waste. With a lean business model, business processes are mapped and analyzed to make improvements across the entire value stream.
To be lean is a broad topic, covering any business operation that works to cut waste whilst also improving business output.
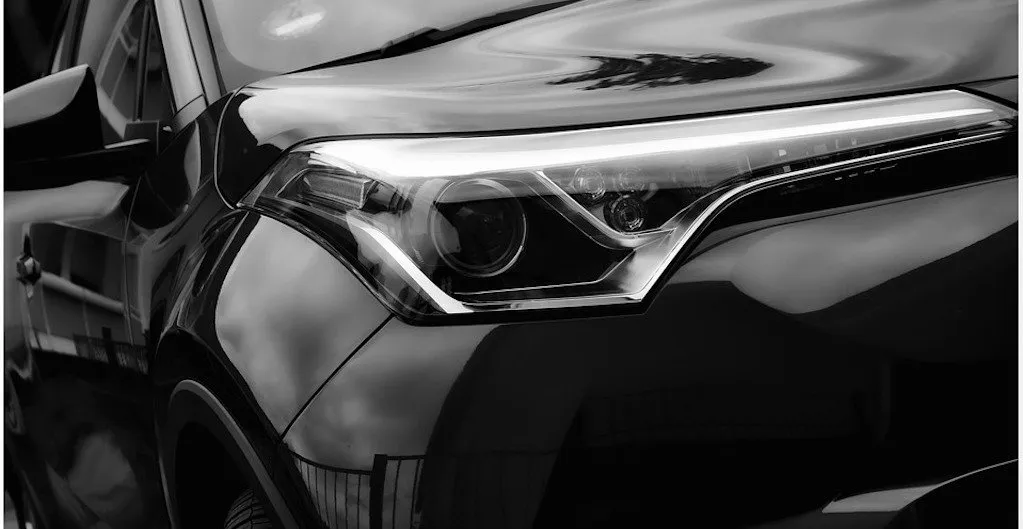
Principles of a lean business were first established in Japan to improve sales and profit. Following World War II, Japan lacked the cash to finance big-batch, large inventory production methods used by other, more developed countries. This issue was exacerbated by a high unemployment rate and a lack of natural resources.
To solve this problem came Japanese industrialist Eiji Toyoda. Toyoda developed the Toyota Production System, often referred to as Just In Time (JIT) Production. JIT was a workflow methodology used by the Toyota automobile manufacturer, that aimed to reduce Toyota’s manufacturing flow times.
So how was the JIT production system lean?
- By explicitly documenting processes that had balanced workflows and diversified skill sets. With these processes came full transparency in regards to what tasks were wasteful, and where output/value could be maximized.
- By reducing turn around time, increasing product/service value for stakeholders.
- By reducing the requirements for raw materials and decreasing waste.
The JIT production system was the first lean manufacturing technique. As such, the term lean is generally used when referencing the manufacturing industry. However, over the years, similar principles have been applied to businesses across a spectrum of industries. That is, lean thinking is used regardless of industry.
The 5 lean principles
Womack and Jones defined 5 main lean principles in their book The Machine that Changed the World. When this book was published in 1990, Toyota was half the size of General Motors. Today, the situation seems to have reversed, with Toyota passing General Motors as the world’s largest automaker. This was all thanks to Toyoda’s work in defining the lean manufacturing discipline.
A re-issue of the book contrasts two different business systems – the lean system vs the mass system. A comprehensive description of the entire lean system is given based on Womack and Jones’s large and thorough study.
From this study, 5 lean principles are established, namely:
- Value is identified as perceived by the customer: Value is only meaningful when expressed in terms of a specific product or service that meets the customer’s needs at a given time.
- The value stream is identified and created: A value stream is all the actions required to bring the product or service from the raw materials to the customer.
- Value flow is given: Products should flow through a lean organization at a rate to meet customer needs, without delays.
- Pull production not push: Only make as required to meet the customer’s actual demand.
- Striving for perfection: Perfection is about delivering exactly what the customer wants, when the customer needs it and given at a fair price with minimum waste.
Being lean in business begins with the application of these 5 principles. If this application initially seems daunting to you, don’t worry as there are many lean tools out there to help.
Lean tools: Our top 8 lean tools to assist lean principle application
To be lean needs the successful application of the above 5 key lean principles. To assist you with this, we at Process Street are here to help. We have cut through the dross to give you our top 8 lean tools. These are tools proven effective for the correct application of lean philosophy.
What are the lean tools?
Lean tools are methodologies applied in business that assist organizations in becoming leaner.
We already know what to term lean means. But in case you need it, the quote below provides a re-cap.
“Lean is both a philosophy and a discipline which, at its core, increases access to information to ensure responsible decision making in the service of creating customer value” – Jim Bensen
Lean tools were developed as a temporary solution to help a given organization solve a problem. However, many of these tools were definitive and themselves became the problem – e.g. Standard Work System (SWS) and Control and Fabrication Instructions (CFI).
Therefore, it is important to separate the lean tools that work from the tools that don’t. Luckily for you, we at Process Street have already done this, giving you our top 8 lean tools and how you can apply them using Process Street’s pre-made, free, templates.
Lean tool #1: Standardized work
Lean principle/s targeted:
- Value flow is given: Identifies and improves value flow by reducing error and increasing efficiency.
- Striving for perfection: Helps an organization strive for perfection by removing lean roadblocks and encouraging continuous improvement.
Standardized work is one of the most powerful but least used lean tools. As a tool, standardized work makes continuous improvements within an organization. Best practices are documented and adapted to establish new improved standards.
To standardize your organizational operations, we at Process Street recommend you start by documenting your processes. Documenting business processes gives an organization the transparency needed to analyze operations for improvements that work to cut waste and optimize value.
In addition, having standardized processes improves consistency for employees, reduces human error, and mitigates risk.
A business process is a collection of related tasks, that when performed together in a given order, deliver the desired end product or service.
Find out how you can document, optimize, and improve processes for a leaner approach to business via reading:
- How to Write Process Documentation That Helps Your Business Scale (in 5 Steps)
- What is BPM? The Ultimate Guide to Getting Started
- Business Process Optimization: How to Improve Workflows Like a Pro (Free Templates!)
- Ultimate SOP Guide: Standard Operating Procedures Made Easy (Free Templates!)
As you may have noticed, standardized work as lean tool #1 echoes a lot of what we do here at Process Street. Process Street is designed for process documentation and therefore the creation of standard procedures/work.
Why not try our ISO-9000 Structure Template to help you build your standard procedures/work.
Click here to access our ISO-9000 Structure Template!
Lean tool #2: PDCA Cycle
Lean principle/s targeted:
- Striving for perfection: The PDCA cycle is specifically designed for making continuous improvements.
The Plan-Do-Check-Act cycle is an iterative four-step process, designed to manage business operations for continuous improvement. It is also known as the Demming circle.
The PDCA Cycle was first introduced by Walter Shewhart and then later developed in the 1950s by W. Edwards Demming.
The method is simple yet effective, helping to solve organizational problems. With the PDCA cycle, a structure is given for experimental learning, and improvements are tested to measure their effectiveness in helping an organization become leaner. Quality is ensured via the removal of defects and poor practice.
For instance, the application of the PDCA cycle has been found to reduce errors and the waste associated by up to 65%.
To hammer home the point, another case study looked at an electronic manufacturing company in Tijuana, Mexico during a time when the organization experienced an increased product demand. This greater output need caused defects to arise during the manufacturing process. The application of the PDCA cycle in this instance reduced defects by up to 79%.
Use our PDCA Cycle Change Management Model Process Checklist to incorporate lean tool #2 into your lean-approach.
Click here to access our PDCA Cycle Change Management Model Process Checklist!
Lean tool #3: 5 Whys
Lean principle/s targeted:
- Striving for perfection: Like the PDCA cycle, the 5 Whys looks at issues associated with a lack of established lean processes and acts to remove these problems.
Toyota Industries is central to the lean philosophy concept. For one, lean manufacturing processes were first established and implemented via Toyota as already discussed above .
Also, in a push to become leaner and leaner, Sakichi Toyoda, the founder of Toyota Industries, developed the 5 Whys approach, which has since become extremely popular across the globe.
Applying the 5 Whys as a lean tool gets to the root of a business-related problem. For the problem/issue faced, why is asked 5 times before a solution is drawn. In this instance, the given solution creates slicker and leaner business operations.
The 5 Whys gives a fact-based and structured approach to problem identification and correction to eliminate operational defects. By doing so, waste is significantly diminished.
“The basis of Toyota’s scientific approach is to ask why five times whenever we find a problem … By repeating why five times, the nature of the problem as well as its solution becomes clear. The solution, or the how-to, is designated as ‘1H.’ Thus, ‘Five whys equal one how’ (5W=1H)”. – Taiichi Ohno, The Toyota Production System: Beyond Large-Scale Production
Run our 5 Whys Checklist Template when you need to get to the root cause of a business-related problem or issue.
Click here to access our 5 Whys Checklist Template!
Lean tool #4: Hoshin Kanri
Lean principle/s targeted:
- Striving for perfection: Hoshin Kanri is a lean tool that targets strategic planning for continuous improvement.
- A value stream is identified and created: Hoshin Kanri sets a new strategic direction to give marked improvements by establishing change throughout the entire organization. That is, the value stream is identified and improved. All employees, departments, and operations are considered and brought on board to implement leaner strategies. Goals and plans among all levels and functions are integrated into daily operations and the value stream.
Hoshin Kanri is another Japan-born methodology developed in the late 1960s.
The process focuses on continuous improvement and learning, taking a team-wide approach. That is, the methodology gets everyone within an organization involved in the implementation of a given objective. That objective could be to make processes run smoother, reducing waste and becoming leaner.
The effectiveness of Hoshin Kanri as a lean tool is widely recognized and recommended for use in multiple industries, such as healthcare.
For more information on the Hoshin Kanri methodology, read: Hoshin Kanri: Gain a Competitive Advantage With This Lean Management Approach (Free Template).
Use our Hoshin Planning: Hoshin Kanri Policy Deployment Process Checklist to guide you through the Hoshin Kanri planning process.
Click here to access our Hoshin Planning: Hoshin Kanri Policy Deployment Process Checklist!
Lean tool #5: Cascade Strategic Planning
Lean principle/s targeted:
- Striving for perfection: The Cascade Strategic Planning approach is an alternative model to the Hoshin Kanri methodology. Therefore, the lean principles targeted are the same. It is a strategic approach used for continuous improvement and therefore hits the strive for perfection principle.
- A value stream is identified and created: The Cascade Strategic Planning approach also sets new strategic direction to give marked improvements by establishing change throughout the entire organization. For this, the value stream should be identified and improved.
A strategic plan can be thought of as your business roadmap. Gaps are identified between an organization’s current state – so inefficiencies, bottlenecks, wasted resources, etc – and its desired future state – a super-lean process. A strategy is then defined. Putting this strategy into action is, however, is the most difficult bit, with 90% of organizations failing to execute their strategies.
Luckily there are tools and techniques out there to assist the application of new corporate strategy. When this new strategy = stellar operations, you can see how models for strategy implementation – Hoshin Kanri and Cascade Strategic Planning – also function as lean tools.
Use our Strategic Planning Template to plan, define, and document your business strategy. Adopt a flexible and inclusive approach by implementing the Cascade Strategic Planning Model.
Click here to access our Strategic Planning Template!
Lean tool #6: Root Cause Analysis
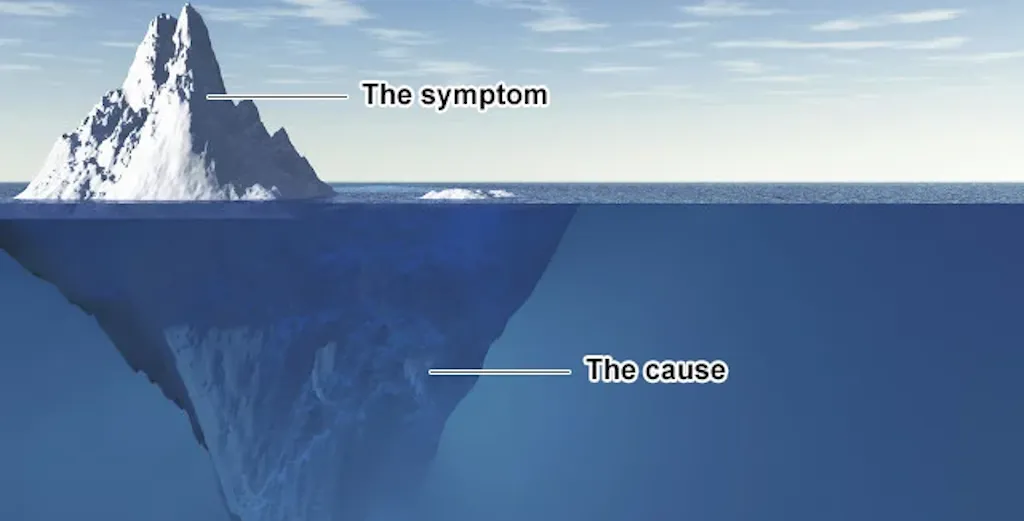
Lean principle/s targeted:
- Striving for perfection: Root cause analysis defines the cause of quality/productivity-related issues in business. When the cause is removed, business improvements are firmly established.
- Value flow is given: If the products/services are not flowing through the organization as they should (due to bottlenecks and delays), RCA can be used to target the problematic areas from the core to establish a smoother value flow.
If you break a bone, what do you do?
I had the delightful experience of shattering my finger a few years back. I knew my finger was broken because I experienced the typical symptoms of a broken bone. Aka, pain, nausea, and low blood sugar – the latter two being from shock. I took pain killers and ate to give my blood sugar a boost. However, these actions only served to treat the symptoms and not the root cause. For the latter, I needed an operation, multiple hospital visits, and physiotherapy.
The same principles apply when treating a problem at work. That is, treating symptoms does not fix the problem and could even make it worse – aka my finger would have turned septic without quick treatment. Root cause analysis (RCA) is a popular and often-used technique to find out what caused the problem in the first place. A specific set of steps are followed which vary depending on the RCA approach taken.
In this instance, the problem is the over-use of business resources and too much waste when delivering business value. Implementing RCA means efforts are targeted for a leaner business. Studies show RCA can reduce business waste by up to 50%.
In our Root Cause Analysis Template the Fishbone diagram (Ishikawa diagram) is used to help you dig deep and identify the root cause of a given problem.
Click here to access our Root Cause Analysis Template!
Lean tool #7: SMART Goal Setting Checklist
Lean principle/s targeted:
- All principles. SMART goal setting is an easy way to set and achieve goals to deliver on all 5 lean principles: Identification of value perceived by the customer; identifying and creating a value stream; establishing a smoother value flow; creating product/services based on pull production not push, and striving for perfection.
The SMART method is an excellent approach to setting achievable goals because it covers all bases, and leaves no room for misunderstanding.
SMART stands for:
- Specific
- Measurable
- Attainable
- Relevant
- Time-bound
For a leaner approach to business, new goals are needed. These goals could include, reduce operational waste by X%, reduce energy costs by X, or launch product update.
Running a checklist like our SMART Goal Setting Checklist means your goals are set and documented, and motivation to obtain these goals are maintained until they are reached.
Click here to access our SMART Goal Setting Checklist!
Lean Tool #8: Environmental Management System (EMS) Implementation Checklist
Lean principle/s targeted:
- Value is identified as perceived by the customer: From generation Z to generation X, over half of the population will pay more for eco-friendly products, with 61% of Millenials willing to pay more for sustainable alternatives. Establishing an effective Environmental Management System caters to this eco-conscious customer.
- A value stream is identified and created: Green production systems require efficient production and low resource use. An Environmental Management System (EMS) supports the use of Environmental Value Stream Mapping (Environmental-VSM), which identifies waste, reduces process cycle times, and implements process improvements in the value stream for leaner procedures.
- Pull production not push: An Environmental Management System focusses on product development and not on the product characteristics alone. It looks to improve the entire product life cycle, thinking about this life-cycle holistically. This includes accounting for demand so a surplus of products/services are not wastefully produced.
Becoming leaner often runs hand-in-hand with business sustainability. Think about it, to be more sustainable, organizations must demand less, run more efficiently yet still deliver quality products and services to the consumer.
This is why an Environmental Management System (EMS) makes our top 8 lean tools list. Implementing an Environmental Management System (EMS) improves environmental performance whilst also establishing leaner operations.
Use this Environmental Management System (EMS) Implementation Checklist to help you create a plan for the development and implementation of your EMS.
Click here to access our Environmental Management System checklist!
To access more checklist tools for the development and implementation of an EMS, read: 5 Free ISO 14001 Checklist Templates for Environmental Management.
Lean tools and the benefits they give
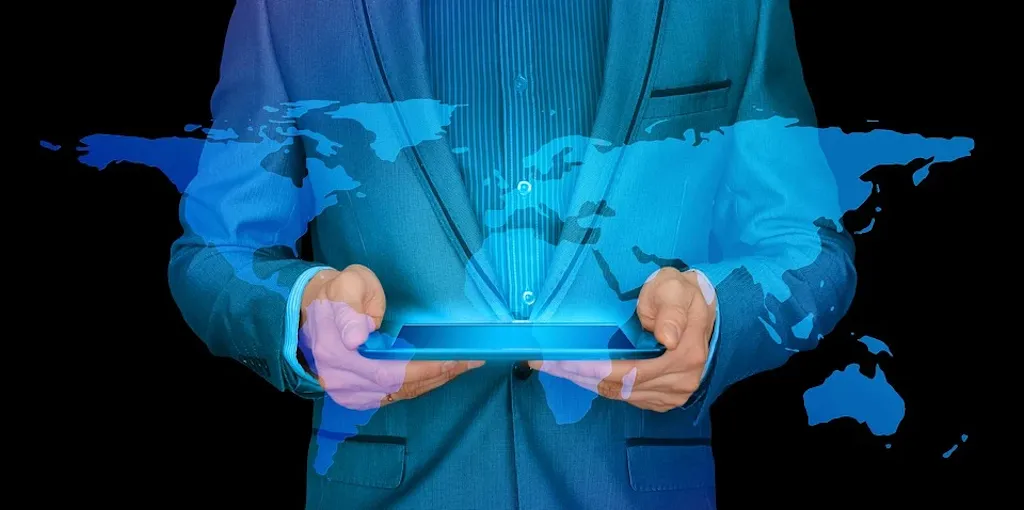
I first understood what it meant to be lean in business during my final year university dissertation.
Lean internationalization was the topic and our project sought to explain how technology was helping start-ups become lean and expanding enterprises.
Eager-eyed and enthusiastic, my team and I (under the supervision of technology venturer Erkko Autio) interviewed top CEOs to find out their perspectives.
What did we find?
Before I answer that question, what do you think? How do you think technology streamlines operations helping start-ups scale?
I know you’re hungry to find out our results, so I will quickly move on.
Start-up companies across the globe were leveraging technology to adopt lean tools and processes. This meant they needed fewer assets and resources to expand and become operational in new countries and regions. Being lean – via using lean tools – meant the startups we studied had:
- Greater business flexibility
- A sales advantage
- More effective market experimentations
- Superior IP protection
In summary, technology and the lean tools implemented helped organizations establish leaner operations and lean thinking. Other benefits include:
- Improved quality performance,
- Faster turnaround times for targeted processes
- Cost reductions and profit improvements
- Increased productivity
Technology gives businesses a platform to implement lean tools. But, our findings also support the idea that technology itself is a lean tool in its own right. I expand on this idea below.
Process Street and Zapier: Lean software tools you should use today
Lean software is software designed to optimize efficiency and minimize waste. In this sense, lean software can be thought of as a specific sub-branch to the concept of lean tools. Lean software exemplifies how technology can be deployed as a lean tool.
Process Street and Zapier are two tools defined under the concept lean software. You can use both Process Street and Zapier to establish leaner processes in your business or line of work. We have already seen how, with Process Street, you can document your business processes and apply top lean tools via our superpowered checklists.
Process Street and Zapier come into their prime, however, when utilizing automation.
With Zapier you can automatically find and run checklists in Process Street, to then trigger actions in over 1,500 apps, including Salesforce, Slack, Airtable, and Google Documents. For more information on how you can do this read: Using Zapier to connect to other applications and automate your processes.
These integrations are extremely handy, especially considering that, according to McKinsey, ~half of your work could be automated. Automation cuts business costs by up to 90%, establishing a leaner business and processes.
For more information on Business Process Automation, read: The Ultimate Guide to Business Process Automation.
Setting yourself up with Process Street
Process Street is superpowered checklists.
So far I have introduced you to 8 top lean tools and their associated Process Street checklists. As you work through these checklists you will come across features such as:
- Stop tasks to ensure task order. This reduces the error that comes from missing out vital steps in a given process. Reducing error reduces waste for a leaner approach.
- Dynamic due dates, so no deadline is missed, keeping projects and processes on track to improve value flow.
- Role assignments, to ease task delegation within your team. Tasks can be assigned out automatically to individuals, streamlining, and synchronizing work within a given team.
- Approvals, allowing decision-makers to give the go-ahead (or rejection) on important items. Also, the necessary comments can be provided. Individuals assigned for approval are automatically notified when this approval is needed, reducing time wasted contacting the relevant personnel for a slicker process.
- Task assignments, to assign users and groups to individual tasks in your checklists. This makes it easy to see who is responsible for what, enhancing team productivity and therefore value output for leaner processes.
- Embed Widget, allowing you to view and interact with other apps without leaving your checklist, automating steps that would otherwise sap your time.
As you can tell, Process Street as a lean software comes jam-packed with features that make any business process, whether this process applies a specific lean tool or not, leaner.
That is, Process Street helps apply lean tools to business.
Process Street, as a lean software, is a lean tool in its own right.
Moving on from this last point, you can transcribe any business process in a Process Street checklist, for free.
Simply sign up for Process Street today and get started!
For more information on how you can create and edit templates in Process Street, watch the below video: Basics of Creating and Editing Templates.
Use lean tools, such as Process Steet, to maximize stakeholder value and minimize business waste
Using the top 8 lean tools presented in this article will help you effectively apply lean philosophy for your business or line of work.
Lean philosophy is unjustly treated with caution due to the investment needed. However, when applied thoroughly and correctly, being lean in business can bridge the difference between success and failure. Don’t be a fear victim and shy away from lean methods that are proven successful.
What lean tools do you use in your business or line of work? What challenges and successes have you faced? We would love to hear from you, so please comment below.